Manufacturing
Supply Chain Services
Manufacturing
Today’s manufacturers face intense pressure to balance cost, quality, flexibility, customization and product delivery time. They need access to data and the ability to analyze and plan around it. Alpine Supply Chain Solutions Supply Chain Manufacturing Services equips them to do so. Each engagement begins with a Best Practice Assessment and ends with a cost justifiable solution.
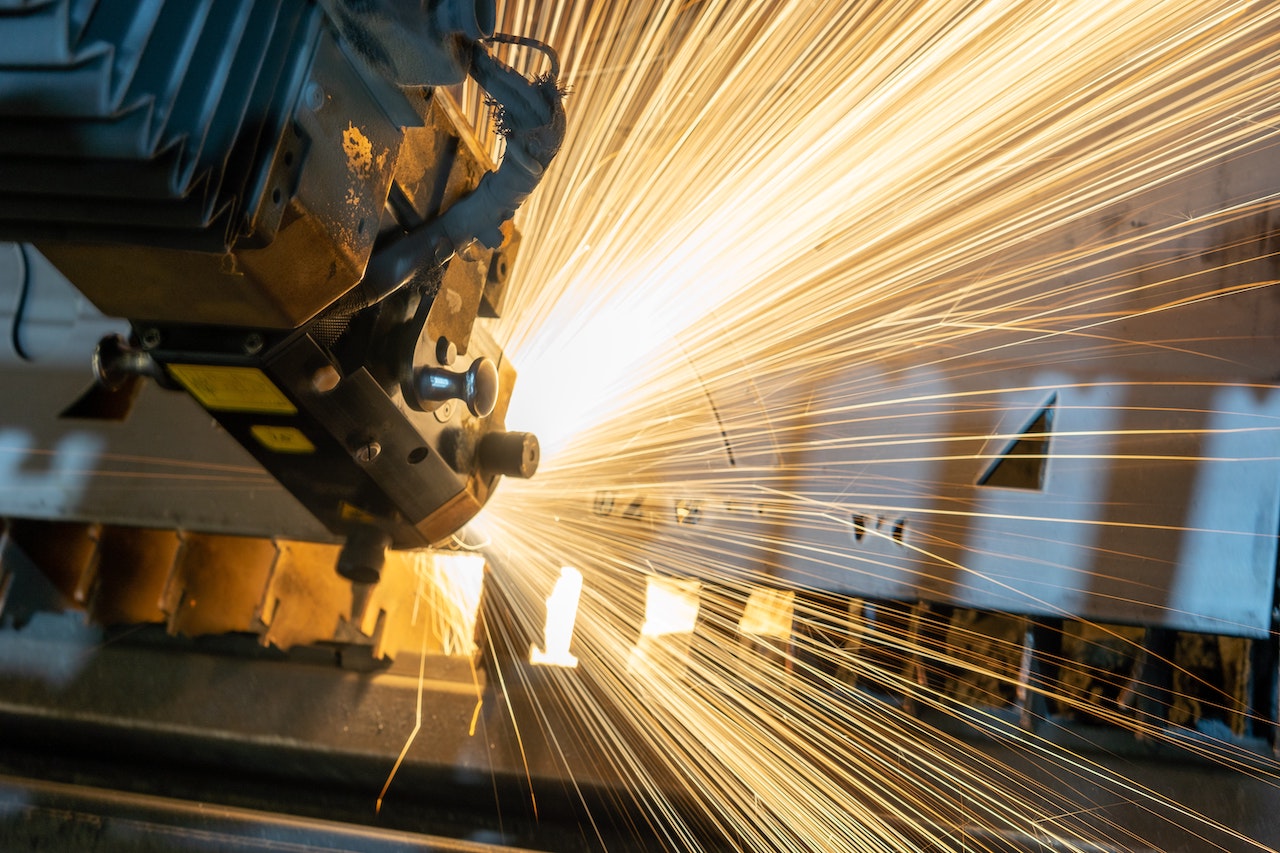
Plan for Every Part
Capacity Planning
Supplier Sourcing & Audits
Inbound Process
Facility Layout
Finished Goods Planning
End to End Relational Modeling
Discrete Event Simulations
Plan for Every Part
Plan for Every Part (PFEP) defines a plan for each part in your supply chain. This plan can include component sources, order frequency and volume, receiving procedures, put-a-way and retrieval processes, storage and equipment requirements, and flow to assembly practices. PFEP is driven by an explosion of the Bill of Materials and linked to your Sales and Operations Plan. A comprehensive PFEP models around the relationship between component supplies and the demand for finished goods, including distribution and the fulfillment of customer orders.
Capacity Planning
During this process we will analyze your existing capacity, consider assembly and value add requirements, explore component sizing and identify any opportunities for consolidation, and plan for future needs. The resulting plan will equip you to balance inventory, efficiently store every part, deliver with confidence and scale with ease.
Supplier Sourcing & Audits
Supplier Sourcing & Audits will help you re-evaluate and improve your company’s purchasing activities. This process enables you to build an effective sourcing strategy that balances price, availability, service, and quality. Our ultimate goal is to help you achieve the lowest Total Cost of Ownership (TCO) alongside minimal supply chain risk.
Inbound Process
An Inbound Process review will enable you to map out a reliable, controlled flow of materials to increase your company’s performance and eliminate unnecessary expenses. Together, we’ll examine component demand, minimum order quantities, distance to source, lead times and other parameters to optimize the movement of goods from suppliers to the plant.
Facility Design & Layout
Alpine’s Facility Design & Layout approach ensures smooth flow of work, material, and information through your facility by considering:
Facility Parameters
Component Size & Packaging
Cost, Service & Productivity
The layout design process always incorporates safety. The design should enhance your Associates work experience. Eliminating blind spots, designing proper aisle widths, traveling in straight lines, minimizing the need for Associates to bend or turn, incorporating visual management, and identifying pedestrian walkways are all ways we build safety into the design.
Component Demand
Assembly Requirements
Finished Goods Planning
Struggling to balance on time delivery and inventory objectives? Holding too much inventory of one thing and not enough of another? With Finished Good Planning, you can evaluate market expectations, response times, demand by region, partner networks and more to design a balanced distribution network that ensures you hold the right amount of inventory in the right location while retaining the ability to scale as needed.
End to End Relational Modeling
Liberate your data with end to end relational modeling. Quickly access and assemble data from multiple sources and transform it into decision-driving information that enables you to optimize your supply chain. Gain visibility into:
- Component Sourcing
- Inbound Flow
- Facility and Component Flow
- Value Add and Assembly
- Finished Goods Distribution
- And more…
Improve the way you communicate, collaborate, act and react.
Discrete Event Simulations
The right decision-making approach is tough to nail down in a manufacturing environment. Heuristic techniques won’t yield optimal models, but discrete event simulations will. With a discrete event simulation, you can measure, test, report and adjust any element within your “end to end” supply chain.