by Noelle Abarelli | Jun 17, 2023 | Alpine News Blog
NAPLES, FL — June 16, 2023 — Alpine Supply Chain Solutions, a boutique consulting firm focused on maximizing supply chain investments, today announced the company has been named a recipient of the Top Supply Chain Projects Award for 2023 by Supply & Demand Chain Executive.
Alpine Supply Chain Solutions received this award for its work with MONAT Global, an international, healthy-aging haircare, skincare, and wellness innovator, in its effort to modernize its distribution operations to support rapid and ongoing growth.
The Top Supply Chain Projects Award (formerly known as SDCE 100) highlights jaw-dropping transformation projects that deliver much-needed value to small, medium, and large enterprises across a range of supply chain functions. It’s projects like these that demonstrate how supply chain solutions and service providers are essential in helping their customers and clients achieve supply chain excellence while preparing their supply chains for success.
When Alpine initially engaged with MONAT, the company was running three facilities that were bursting at the seams. MONAT originally had its eye on revamping one of these operations, but Alpine’s analysis of their peak season performance led the team to determine that building a new facility near the company’s headquarters in Doral, Florida would yield the most rapid benefits.
Alpine led the design of the new facility packed with clever storage solutions and automated technology that would enable MONAT to distribute more product efficiently. Shortly after go-live, results included productivity and cost savings. Outbound shipping rates increased from 80 lines/hour to 120 lines/hour, throughput rates went from 38 units/hour to 60 units/hour, and the receiving and putaway went from processing 6.6 pallets/hour to 40 pallets/hour.
“From demand planning and forecasting to implementing the ultimate in warehouse automation, the past 12 months has seen companies within the supply chain and logistics space upgrade, enhance, adopt, and adapt in order to achieve greater efficiency along the chain,” says Marina Mayer, Editor-in-Chief of Supply & Demand Chain Executive and Food Logistics. “That’s why it’s important today’s supply chains run on collaboration.”
“Companies partnered to implement each others’ software and technology and work smarter, together. And, it’s these partnerships that have enabled many supply chain organizations to better manage inventory, reduce costs, retain employees, track data and analytics, and build resilience for whatever disruptions may lie ahead,” Mayer adds.
“Alpine is honored that SDCE selected this project as an award winner,” said Alpine Managing Principal, Michael Wohlwend. “We are thrilled to be a small part of the important work MONAT is doing to provide premier, sustainable products and entrepreneurial opportunities across the globe.”
To view the full list of Top Supply Chain Projects winners, go to www.SDCExec.com/awards.
About Alpine Supply Chain Solutions
Alpine Supply Chain Solutions, based in Naples, FL, is a supply chain consulting company driven to ensure their clients get the most value from their investments. Their approach to every project starts with the data and ends with a cost justifiable solution. With deep roots in industrial engineering, Alpine’s approach is unique. For more information, please visit: http://www.AlpineSupplyChain.com
About Supply & Demand Chain Executive
Supply & Demand Chain Executive is the only supply chain publication covering the entire global supply chain, focusing on trucking, warehousing, packaging, procurement, risk management, professional development and more. Supply & Demand Chain Executive and sister publication Food Logistics also operate SCN Summit and Women in Supply Chain Forum. Go to www.SDCExec.com <http://www.sdcexec.com/> to learn more.
by Noelle Abarelli | Jun 13, 2023 | Alpine News Blog, Warehouse Consulting News
The Northeast’s largest mattress and furniture retailer, Raymour & Flanigan has been synonymous with exceptional quality and service for over 70 years. With four main distribution centers (DCs) and 22 forward DCs that ship furniture to customers, warehouse operations play a critical role in their success. That’s why when Raymour & Flanigan set out to revolutionize their warehouse operations, they partnered with Alpine Supply Chain Solutions for help. Learn how they are elevating the customer experience with cutting-edge WMS modernization.
The need
Raymour & Flanigan was working with multiple systems; a legacy best-of-breed WMS was being utilized in seven of its complex facilities, and a legacy ERP was being used in the rest. And while this approach provided high-quality fulfillment services to its customers, it was not always delivered efficiently. One clear example of inefficiency is how sometimes an item would pass through three different DCs before being delivered to a customer. Imagine how much happier the customer would be without all the unnecessary travel. Not to mention that certain putaway procedures were performed without visibility into downstream demand, which could present several challenges:
- Inefficient inventory management
- Poor supply chain coordination
- Inaccurate demand forecasting
- Increased lead times
- Ineffective production planning
- Reactive decision-making
- Customer dissatisfaction
There was a lot of room for improvement.
The process
Selecting a WMS is a large undertaking and one that requires due diligence. With a Best Practice Assessment (BPA) and Storage Type Analysis (STA), Alpine Supply Chain Solutions learned that a highly-adaptable WMS would be able to realize productivity improvements that would support Raymour & Flanigan’s future growth and success. With insight into current and future requirements, space utilization, safety, and flow, Raymour & Flanigan chose Körber Warehouse Advantage (WA) to serve as its new WMS. The system enables system-directed put-away and picking, opportunistic cross-docking, and increased storage capacity through better cube utilization and advanced processes. Another crucial factor in their decision was knowing WAs scalability and the ability to easily replicate the implementation process in multiple sites.
The result
To start, Raymour & Flanigan chose to roll out the Körber WA in one of their less complex warehouses. With this approach, they can better understand the system’s capabilities and features so they can implement exactly what they need when the time is right. The plan is to eventually have all 22 sites on the new system, with expected benefits of:
- Increased storage capacity
- Efficient inbound handling
- Opportunistic cross-docking
- Improved inventory visibility
- Picking efficiencies
- Loading accuracy
Raymour & Flanigan’s investment in Körber WA for WMS implementation aligns perfectly with their goals of enhancing productivity, reducing expenses, and eliminating tracking gaps. By embracing this solution, they are ready to unlock a new era of operational efficiency and customer satisfaction.
For more details on their selection process and journey, visit Logistics Viewpoints. If you’re looking for optimal solutions that drive maximum value to get the most out of your supply chain, Alpine Supply Chain Solutions can help. Reach out today!
by Noelle Abarelli | Jun 5, 2023 | Alpine News Blog
It’s summertime, and for all of us at Alpine Supply Chain Solutions, that means that we get another chance to mentor the next generation of supply chain leaders. We’re excited to welcome four supply chain interns this summer: Robby Griffin, Drew McDermott, Hema Sai Ari, and Nader Nouwairi. Our internship program is focused on helping college students and recent graduates get hands-on supply chain experience.
During their internship, Robby, Dew, Hema, and Nader will connect with and learn from one another, Alpine’s leadership team, and our growing list of clients. The supply chain world is always looking for new and innovative ways to solve problems, and we’re confident that these interns are going to teach us just as much as we teach them!
Here’s a little more about our 2023 interns:
Robby Griffin
Robby Griffin just completed his junior year at Michigan State University (MSU) and is pursuing a bachelor’s degree in Supply Chain Management. He is part of the MSU Supply Chain Management Association Executive Board and will be the Chief Financial Officer this coming year. Robby is looking forward to growing his knowledge of Supply Chain Management with the help of Alpine in his role as a Supply Chain Process Intern. Previous experience includes serving as a Warehouse Employee at Griffin Beverage and a Customer Solutions internship at McCain Foods.
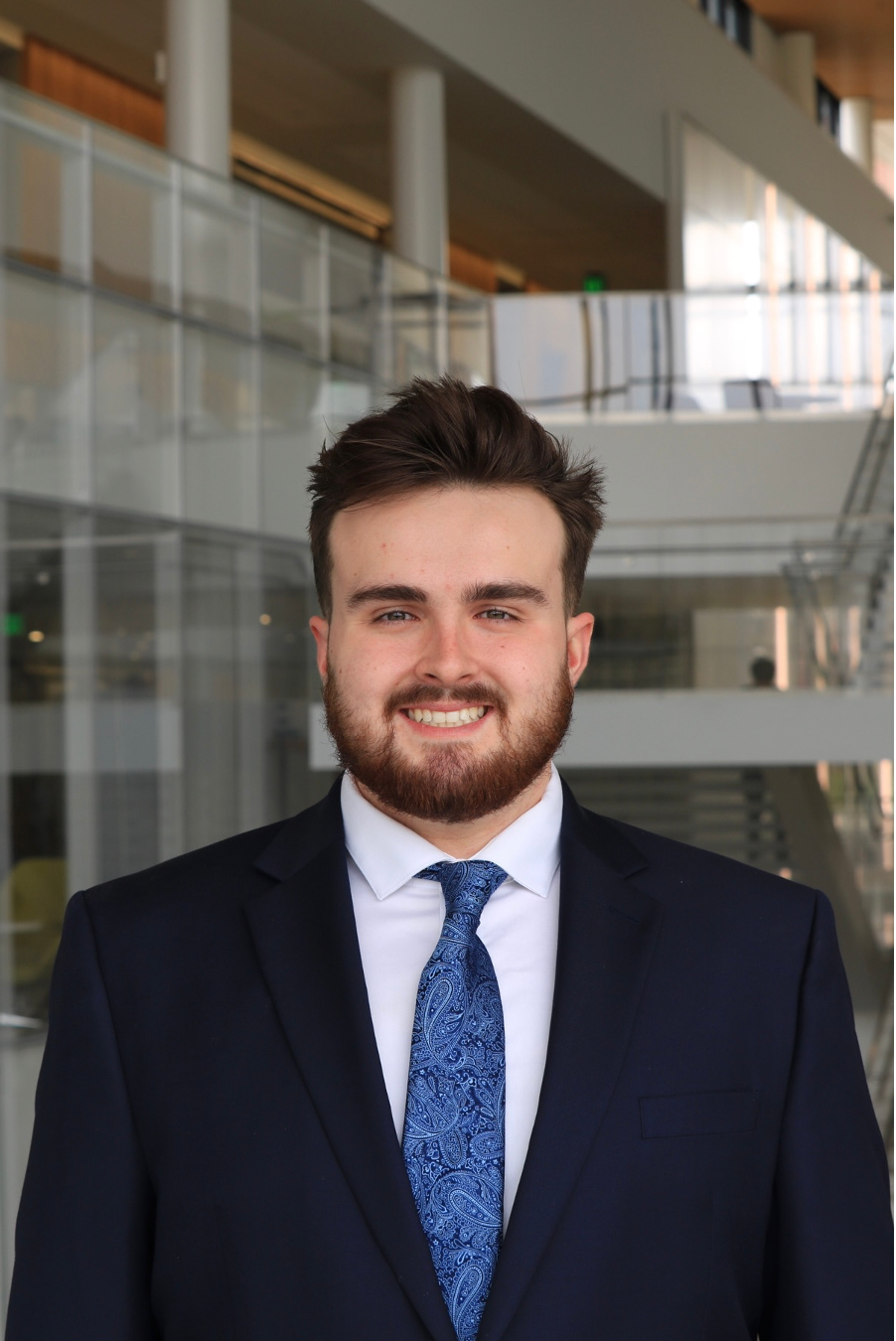
Drew McDermott
Drew is a Summer Business Development Intern at Alpine and he is excited to explore as much of the world of supply chain systems as possible. He is currently a junior at Northwestern University, where he studies Economics and Political Science. In addition to his studies, Drew serves as Vice President of the Northwestern Rugby Football Club, is a member of Northwestern’s Sports Analytics Group, and loves outdoor activities.
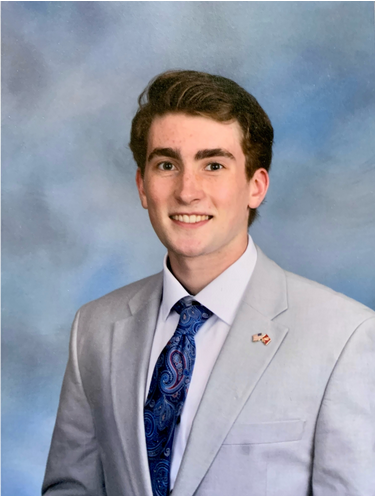
Hema Sai Ari
Hema Sai, an individual driven by an insatiable hunger for knowledge and self-improvement, will serve as a Data Engineer Intern at Alpine this summer. A senior-year project on self-driving cars ignited Hema’s fascination with data analytics and propelled them into the realm of data-driven decision-making.
After honing their skills and gaining invaluable experience as a Junior Data Engineer at a prominent software service-providing company, Hema recognized the need to expand their expertise which is what prompted the decision to pursue a Master’s degree in Business Analytics and Information Systems at the University of South Florida.
To date, Hema has made notable contributions as a University Innovation Fellow, receiving comprehensive training in design thinking and product development from Stanford University. Their leadership qualities were showcased as they took the helm as President and Spokesperson for the Mechanical Engineering Student Body, effectively representing their peers and championing their interests. As a Data Engineer Intern at Alpine this summer, Hema will bring an unrivaled drive for excellence, a profound understanding of data analytics, and a profound dedication to achieving exceptional results.
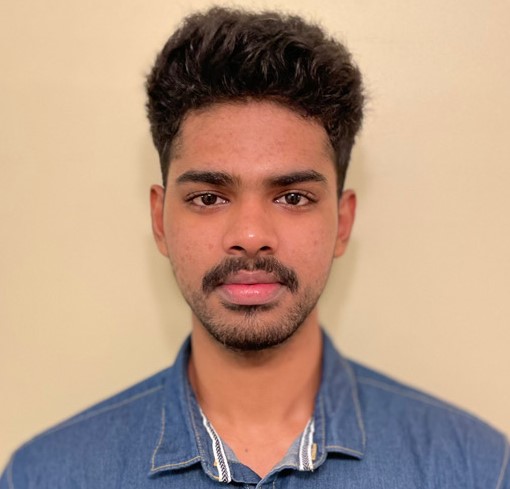
Nader Nouwairi
Nader received his Bachelor’s in Supply Chain Management from Western Illinois University. Currently, he is pursuing his Master’s in Supply Chain Management from WIU and will be graduating in Fall 2023. Over the summer he will be working as Supply Chain Process Intern. He is excited for the opportunity to visit a variety of different clients and take on the different challenges that arise.
Nader was previously a Supplier Development Intern at a high-risk supplier organization where he focused on ensuring capacity for the following fiscal year’s demand. He also took on updating commodity indexes and creating action plans for high-risk suppliers. Through his experiences, he has found a desire to analyze data and implement new solutions to improve upon existing supply chains.
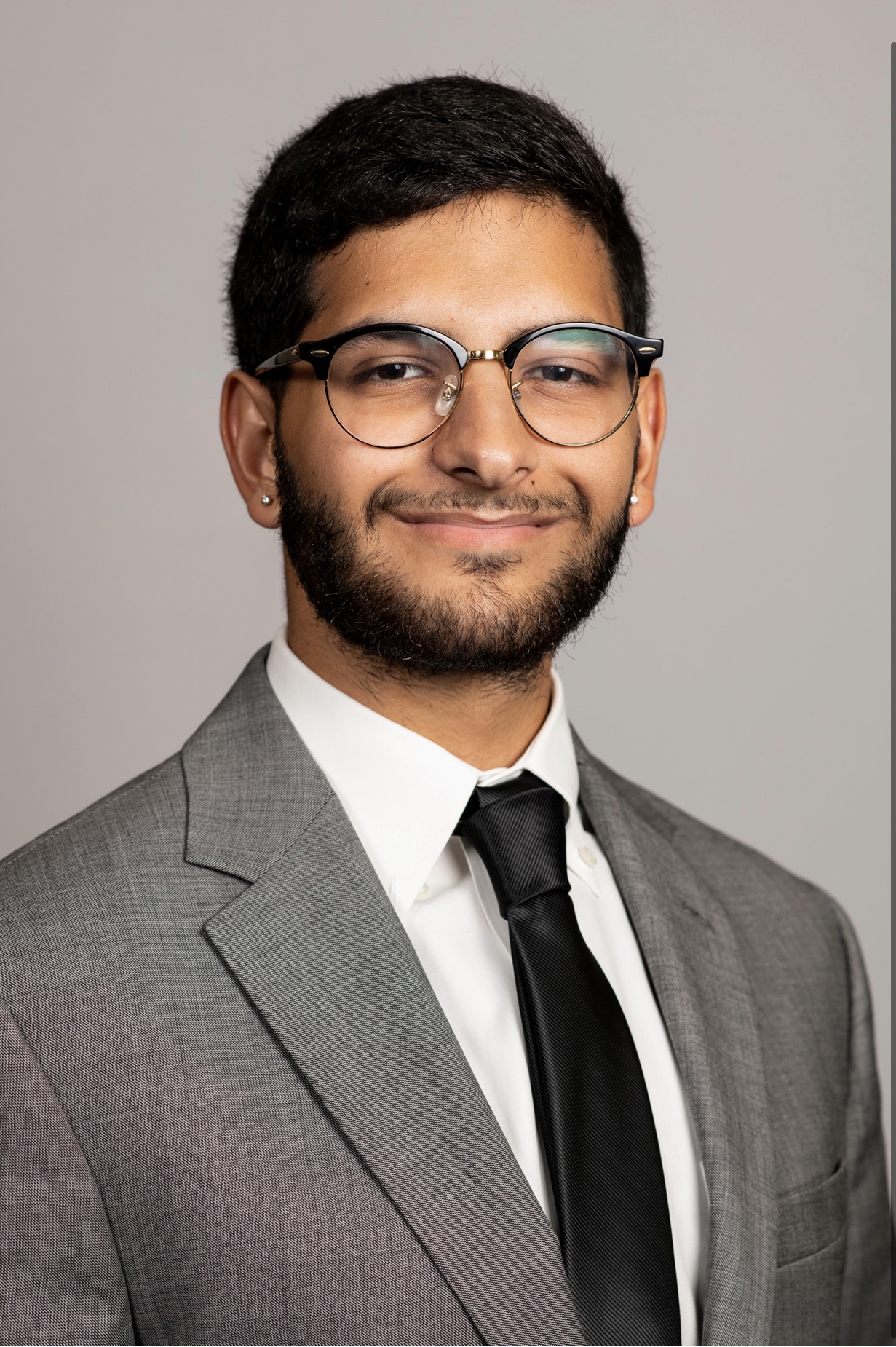
by Noelle Abarelli | May 22, 2023 | Uncategorized
Founded in 1960, Dexter Group is a premier supplier of axles, suspension, brakes, doors, venting products, trailer parts and accessories, and towing components serving the commercial trailer, RV, heavy-duty, marine, agriculture, and manufactured housing markets.
Alpine is proud to be partnering with Dexter on Project LEAP – a large-scale ERP development and implementation project. Project LEAP began as a WMS implementation, but as Dexter acquired new business units and brought them into their distribution network, the project evolved into something greater crafted with a focus on four key elements:
- Learning
- Equipment
- Advancement
- Progress
The project’s goal is to bring Dexter together as one entity so that all branches can work together in one system fostering cross-functional alignment. This gives both employees and customers the ability to view product availability from all over the country, empowering the Dexter Group to serve their customers holistically, in a way they were not able to do when using multiple ERP systems.
Launching Project LEAP across different sites, branches, and personnel, involved a huge collaborative effort, but it’s been well worth the work. With all teams involved it means every department has representation and a say in the process, from sales, marketing, and product development, to purchasing, inventory control, and branch managers.
The benefits of merging all branches into one system are many:
- Better growth opportunities
- Improved visibility throughout branches
- Flexibility to scale with customer needs
- Ability to look into inventory from portable RF devices
- Reducing the number of steps needed to get orders out the door
- Warehouse duties can be better distributed and organized as needed
Watch this video to learn more about Project LEAP, and to get tips on how to successfully manage a large implementation project of your own. If you’re looking for optimal solutions that drive maximum value to get the most out of your supply chain, Alpine Supply Chain Solutions can help. Reach out today!
by Noelle Abarelli | May 16, 2023 | Uncategorized
This post about Alpine Supply Chain Solutions & Ecentria is taken from SupplyChainBrain, written by Russell W. Goodman.
Huge growth in sales led to the need to optimize inventory, fulfillment and warehouse operations at Ecentria, say Michael Wohlwend, managing principal of Alpine Supply Chain Solutions, and Andrew Mironov, head of operations at Ecentria.
Ecentria, an online distributor of high-end technical gear and apparel for outdoor enthusiasts, hunters and law enforcement personnel, experienced sales growth that outstripped storage capability in its distribution centers, says Mironov. “We needed to look at our distribution network as a whole, and make sure that we were properly serving our customers and saving on overhead costs.”
In addition to storage, Alpine analyzed SKU and velocity growth, Wohlwend says. “Coupled with their order profile, we were able to identify justifiable automation solutions. We ended up going with a goods-to-person solution.”
Following that, Alpine performed a distribution network analysis, looking at inbound and outbound transportation costs. The goal was to optimally serve both the East and West Coasts within two days. All analyses were completed within 12 weeks, Wohlwend says.
“From the storage type analysis, we decided to optimize our storage pick faces with some different racking profiles,” Mironov says. “And we also looked into a goods-to-person solution that will sustain us for years to come. When we reviewed our distribution network analysis, we found that our two-DC configuration we currently employ is actually optimal for not only our consumer base, but our supply chain as well.”
In Mironov’s opinion, Ecentria learned quite a bit about its own business from Alpine’s “deep dive.” It gave management “confidence in knowing that our existing distribution network set-up was ideal for our customers.”
The relationship continues, Mironov says. “We are going to be working together to look closely at our slotting arrangement within our warehouse, and making sure the layout is ideal for optimal efficiencies for our labor force.”