Adding ecommerce capabilities to a traditional retailer’s warehouse – If your warehouse is designed for Put-to-Store, Flow through, or Batch Pick & Sort by Store strategies, new capabilities to fulfill online orders include picking eaches, processing orders with very few lines, parcel shipping, and managing tight cutoff times.
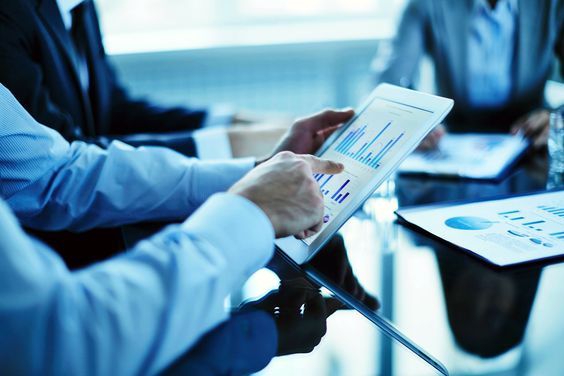
Cutting Costs & Maximizing Results: Understand Your Operation
Have you ever heard the saying, “You can’t see through the woods, when you are in the forest”? This is exactly what happens when you spend 40,50, or 60 hours a week executing your daily tasks. It is not until you look at your operations through different lenses, that you might be able to indentify the low hanging fruit. Sometimes just having a consultant come in and spend a day with you understanding your operations can provide you a punch list of 10 items that you can implement on your own that require very little captial to help reduce costs and maximize results in your operation.
Alpine Supply Chain Solutions offers Warehouse Consulting Services to maximize your facilities space, equipment, labor & control. We start with the data and end with a justifiable solution.