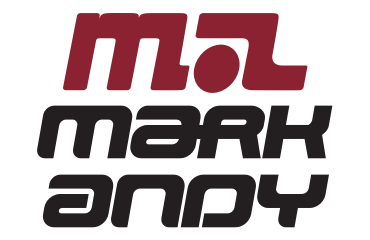
Alpine Supply Chain Solutions Optimizes Distribution for Mark Andy
Performs Storage Type Analysis and Facility Design to right-size facility then a Network
Analysis, 3PL Selection, and onboard to support next-day delivery
Alpine Supply Chain Solutions, a leading boutique supply chain consulting firm, today announced the successful completion of a multi-faceted distribution optimization project for Mark Andy, a global manufacturer of printing presses. Alpine provided consulting services to improve space utilization, productivity and replenishment cycle times at Mark Andy’s primary distribution center in Des Plaines, IL, and conducted a network analysis to determine the best location for third party logistics (3PL) facilities to facilitate next day shipping for customers.
Mark Andy was outgrowing its 80,000-square foot distribution center and needed to determine if 40,000 or 80,000 additional square feet was needed. Alpine conducted a Storage Type Analysis, Facility Design, and Slotting project to create the right-sized product homes and place the right products into the best locations, maximizing space usage and improving productivity.
“Alpine has a well-rounded team that understands all aspects of supply chain operations as well as current
industry standards,” said Stuart Gallup, Vice President-Commercial Market for Mark Andy Print Products. “They were able to rapidly respond to changing information in a very dynamic environment and provided the best solution at a given cost which increased our ROI.”
In addition to the warehouse optimization project, Mark Andy also recognized the need for new locations across the US to facilitate next-day delivery. Alpine conducted a Network Analysis to understand where Mark Andy customers were located and to determine the ideal number of facilities and inventory levels required to provide their network with a 98% next day service window. Alpine then conducted an in-depth RFP process and helped Mark Andy select and onboard five new 3PL locations in five months.
About Mark Andy
Mark Andy is a pioneer of the graphic arts and printing industry. As the world’s leading manufacturer of
narrow- and mid-web printing and finishing equipment, we supply leading global brands, including Mark Andy and Presstek printing presses, Rotoflex finishing solutions, as well as a complete line of Mark Andy Print Products consumables and pressroom supplies. All products are backed by the largest customer support team in
the industry, minimizing downtime and helping our customers be profitable, efficient and at the forefront of innovation. For more information, visit Mark Andy.
About Alpine Supply Chain Solutions
Alpine Supply Chain Solutions, based in Chicago, IL is a supply chain consulting company driven to ensure their clients get the most value from their investments. Their approach to every project starts with the data and ends with a cost justifiable solution. With deep roots in industrial engineering, Alpine’s approach is unique.